Challenges in Creating a Paperless Supply Chain and How to Overcome Them, According to Experts
Going paperless has many benefits for companies in the logistics and supply chain management (L&SC) space. Among others, these include Improved customer experience Cost savings Faster decision-making More accurate data and recordkeeping Given all these benefits, you might be wondering why such a large segment of the L&SC industry has been slow to digitize processes. In this article, I’ll draw on experts’ insights to explain the challenges in creating a paperless supply chain, both from a company perspective and an industry perspective. Then, I’ll discuss how to overcome those challenges, as well as the benefits of going paperless. Let’s start.
Ready to transform your supply chain?
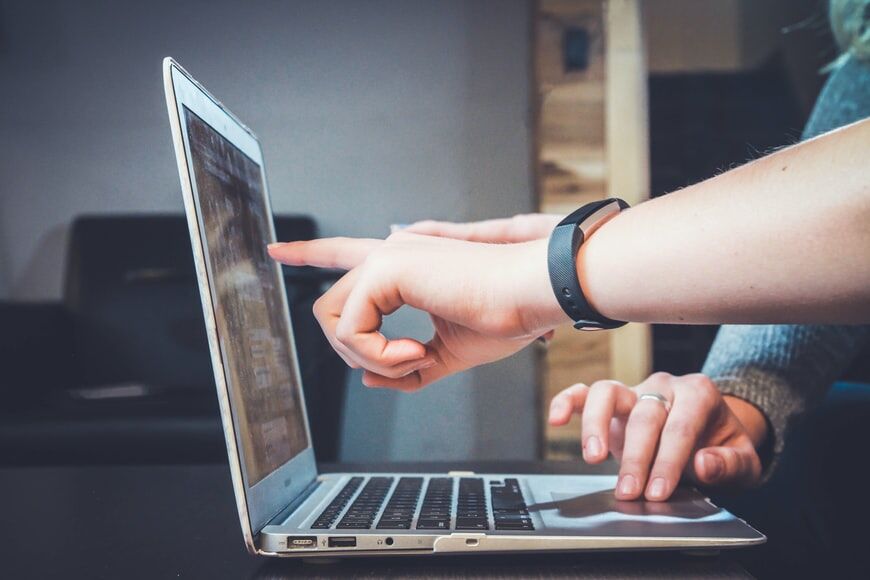
Going paperless has many benefits for companies in the logistics and supply chain management (L&SC) space. Among others, these include
- Improved customer experience
- Cost savings
- Faster decision-making
- More accurate data and recordkeeping
Given all these benefits, you might be wondering why such a large segment of the L&SC industry has been slow to digitize processes.
In this article, I’ll draw on experts’ insights to explain the challenges in creating a paperless supply chain, both from a company perspective and an industry perspective. Then, I’ll discuss how to overcome those challenges, as well as the benefits of going paperless.
Let’s start by looking at what aspects of the industry have and haven’t gone paperless.
The Legacy of Logistics and Supply Chain Management
Even as technology advances at an unprecedented rate in both personal and commercial applications, the adoption of digitalization and paperless technologies, comparatively, has lagged in the L&SC industry.
When asked why that is, Mike Turner, vice president of sales at dynamic freight matching company DFM Data Corp., cited legacy.
“The biggest impediment to going paperless is legacy—legacy systems, legacy processes, legacy people—and I’d say complacency,” Turner said.
Chris Petrocelli, president of xMS Supply Chain Services and an Advisory Board member at the SUNY Maritime College and Oregon State University, seconded that sentiment. He said people get too caught up in the way they’ve always done things. For example, an employee may have been trained to always make two copies of each document and store them in a particular filing cabinet. That employee will be resistant to a scenario where there are no paper copies or filing cabinets.
That mindset of “we’ve always done it this way” causes companies to postpone going paperless.
“As in any scenario, you have the early adopters. And then, on the other end of the equation, you have your laggards. Early adopters assume most of the risk of change; however, they also get the immediate advantages the improvements produce,” Turner said.
Early Adopters: Aspects of the Industry That Have Gone Paperless
Only a small amount of the industry has gone paperless. For example, within the US transportation market, companies that offer digital freight matching services account for just 2%, according to a study by Armstrong & Associates. That number has likely increased slightly since the study was published, Turner said. However, that also means that when a shipper and carrier decide to work together, that pairing is being coordinated manually as much as 98% of the time.
On a smaller scale, different companies have different levels of digitalization, Petrocelli said.
“You’ll find some small companies that might have gone and taken the approach to really work toward eliminating environments where they’re forced to do manual subprocess workarounds,” Petrocelli said. “Companies that have been doing things for a while, it’s just so much harder to change.”
Although there were technological innovations within the L&SC industry in the 19th century, the 1960s and ’70s marked the entry of digital recordkeeping and planning, according to Logmore. Digitalization began to accelerate in the late ’80s as computers became more commonplace.
In the subsequent years, companies increasingly adopted enterprise resource planning (ERP) systems, which aggregate data from multiple sources. Nowadays, almost all L&SC companies use an ERP system, according to RTS. Similarly ubiquitous within L&SC are transportation management systems (TMS), according to the Armstrong & Associates study. Such systems are made more powerful as their creators increasingly equip them with artificial intelligence, machine learning, and predictive analytics, according to RTS.
The industry has seen some automation of manual processes involving warehousing, according to a study by PWC. However, most digitization with the industry has been around paperwork and data.
For example, software enables companies to track deliveries in real time. Drivers can also report accidents or whether a load is over, short, or damaged (OSD).
Similarly, documents like bills of lading (BOLs) and proofs of delivery (PODs) can be converted to a digital format without data loss. Alternatively, they can be filled out and filed without ever having a paper copy. These are all steps toward a paperless supply chain.
Laggards: Aspects of the Industry That Still Need to Go Paperless
Despite 90% of industry experts recognizing the importance of digitization and, more specifically, its benefits in terms of data availability, “the percentage of T&L companies that rated themselves as ‘advanced’ on digitization was just 28%,” according to the PWC study.
What’s sorely needed is the automation of manual tasks like route planning, freight matching, inventory planning, and more. Some companies have already taken steps to create software to do these things. And paperless processes for customer service, invoicing, reporting, and gathering data already exist in many places. But the industry needs to step up its adoption of them significantly.
Old Guards: Aspects of the Industry That Shouldn’t Go Paperless
With so much of the industry still needing to adopt digital processes, there’s a lot of work to be done. So, are there any aspects of L&SC that should remain manual?
Petrocelli suggested developing a manual paper process for something before starting up a new system.
“If you can’t do it manually, how the heck do you automate something?” he said.
But once you know how to implement that process, you shouldn’t consider any aspect of the industry off-limits when going paperless, Turner said.
Impediments to Going Paperless
The lack of standardization across the industry, from the global to the granular perspective, is the biggest impediment to digitization. That lack of standardization—whether across industry sectors, companies, or technologies—creates a problem of communication between groups that otherwise understand the need to collaborate.
Let’s take a closer look at how a lack of standardization impedes a shift to paperless at different levels of the L&SC industry.
(Mis)Communication Between Industry Sectors
At the highest level of the industry, standardization itself is impeding a shift to paperless. The reason is that standardization within different sectors has created a lack of standardization across the industry as a whole. This makes it difficult for different sectors to integrate with one another and create a paperless supply chain, as they can’t standardize documentation such as a BOL.
For example, airlines use alpha codes as identifiers, and ocean carriers use numeric codes, Petrocelli said. This disparity makes it difficult to seamlessly transfer freight from air to ocean, even though airlines and ocean carriers have ports in the same places.
More important, however, is that these different standards make it difficult to implement a universal standard, Petrocelli said. When airlines and steamship lines consider using just one code, the airlines insist that code be alpha, while the ocean carriers insist on using numeric, he said.
The airlines and steamship lines recognize the problem that having different standards creates in the supply chain. However, none wants to give up its preexisting standard for the greater good.
“Getting multiple players to operate together for ‘a greater industry good’—that may or may not affect them positively in the short term—is a high bar to overcome,” Turner said.
(Mis)Communication Between Companies
Just like different sectors of the L&SC have different standards, so do individual companies.
As a product moves through the supply chain, it changes a lot of hands. From the manufacturer to the warehouse to (sometimes multiple) shippers/carriers to the retailer, the product moves across all levels of the supply chain. And each of the parties that interacts with the product has its own standard operating procedure.
“All of them have a different platform, a different way of moving the data, a different security process, a different coding process,” Turner said. And all these different standards have two effects:
- They make it difficult to create a universal, digitized standard that everyone can agree upon and adopt.
- Because there’s no paperless structure across the whole supply chain, these different standards cause a buildup of paperwork every time the product changes hands.
And it’s not just manual processes that cause supply chain problems as companies interact with one another. Often, their technologies are incompatible.
“Although a company can accommodate another company with different processes, they have to come up with a workaround in order to continue to be a supplier of that customer,” Petrocelli said.
(Mis)Communication Between Systems
Technologies that weren’t designed to work together generally don’t. And it isn’t just a problem when multiple companies need to collaborate. Often, the software a single company uses for different departments and tasks are incompatible.
“It’s the pure interaction of systems and the governance that companies have around their ability and inability to do certain types of technical file transfers, for example,” Petrocelli said. “It’s the constraints around existing applications that companies have today. So, they’ve purchased a certain software to manage a certain part of their business, but it doesn’t easily allow for connectivity or integration to other internal systems or externally.”
These incompatibilities are a major impediment to going paperless, but they would also be solved by a universal, digital standard.
“As you think about breaking down aspects of what visibility means across the supply chain, across multiple players, regardless of what platform they use, you can help the overarching system,” Turner said.
How to Overcome the Challenges to a Paperless Supply Chain
Since so little of the L&SC industry has gone paperless, the task of digitizing processes seems monumental. Where do you start?
The key, Turner said, is to start small.
For example, let’s say two businesses decide to collaborate for a shared benefit. They now need to figure out how to get their systems and processes to work together. The biggest impediment here is not making each company’s technologies compatible with the other’s. It’s overcoming a mindset that a company’s data or technology is proprietary and shouldn’t be shared.
“I don’t think anyone here is advocating that you must share 100% of your data in order for things to be effective,” Turner said. What’s needed is “to find a breakthrough to say what piece of data can be shared in a way that is secure, in a way that is confidential, and in a way that makes sense.”
Achieving this is the first step toward creating a paperless supply chain. So, let’s look at how you can encourage that mindset shift.
“A Good Business Case”: How to Get Individual Companies on Board
One reason L&SC is slow to adopt new technologies is because investing in them is a low priority for many companies, Petrocelli said.
“L&SC is the smallest percentage cost of the company’s business—arguably, usually around 10% to 15%. It doesn’t get the priority of commercial activity and doesn’t get the priority of sourcing activity, where you might be spending 50% of the cost of your business,” he said.
That means investments in the area of L&SC are often pushed aside in favor of more immediate concerns, which typically have to do with products or customers, he said.
So, how do you convince the decision-makers at a company that L&SC is worth investing in?
“You’ve got to come up with a good business case,” Petrocelli said. “So, it tends to be around cost savings, efficiency, visibility, better interworking relationships, to support a common customer, so to speak.”
Turner agreed. Whether it’s getting multiple companies to collaborate or getting the stakeholders of a single company on board with going paperless, it’s best to build your argument around the customer’s experience and perspective.
“If you start there, then you can work backward and engage everyone in the organization to view the problem—or opportunity—from a customer experience standpoint,” Turner said. “Through this lens, decision-makers can start to find out where the gaps are appropriate to what might be manual and what might be digital as you identify the touch points that can influence the customer experience.”
And once you get a couple people and companies to see the value of digitizing their L&SC processes, then you can start to build a movement within the industry.
“A Visionary Viewpoint”: How to Get the Broader Industry on Board
One way to achieve digitalization across the L&SC industry is through the intervention of a government agency.
“If you think about dramatic change, there’s always an outside force that drives the desire and willingness of individuals/entities to cooperate,” Turner said. “What we will opportunistically want in the supply chain space is the government to step in.”
The government would decide how to digitize processes. It would also decide what impact that digitalization would have on supply chain touch points. Similar to how federal regulators standardized credit cards, a government agency could implement a paperless L&SC process that would be adopted industrywide, Turner said.
But until that outside force steps in, you once again have to start small.
“It’s getting a small group of like-minded professionals who can see beyond the immediacy of their four walls and really have a visionary viewpoint of the overarching impact of the supply chain itself. And they care about the greater good of the marketplace, as opposed to only what’s happening within their own particular four-wall ecosystem,” Turner said.
One example of such a group is the Contactless Delivery Task Force. In June 2020, the Consumer Brands Association launched the task force in response to COVID-19. The task force includes more than 20 transportation, logistics, and supply chain partners. It seeks to develop standardized, touchless delivery procedures that can be scaled efficiently and adopted by other companies.
Benefits of Going Paperless
Now, let’s take a closer look at the benefits of going paperless.
Broadly speaking, the benefits are
- More accurate data and recordkeeping: As you digitize more processes, there’s less room for human error as staff in the back-office manually enter data from paper files. Additionally, physical documents like PODs are less likely to get damaged or lost. That means your records and data stay intact.
- Faster decision-making: From paperless records comes the level of data and information that you need for analysis of your successes and your pain points. And because it’s all digital, you have easy access to exactly the information you want when you want it.
- Improved customer experience: You’ll be able to use all the data you have to do customer journey mapping. Going paperless enables you to design the best possible customer experience.
- Cost savings: Going paperless doesn’t mean you’ll lose the back-office staff who used to do manual data entry. Instead, you can redirect their time to more value-added projects. That, in turn, means that with the same investment in salaries, you get better work outcomes. Additionally, it will improve employee morale.
You can learn more about how companies have benefited from going paperless here.
Going Paperless Isn’t the Difficult Part
“If you think about the digital processes that we have in place, the trucking industry is far behind most of the industries in reference to adoption,” Turner said. And that means the industry is missing out on the countless benefits that come from going paperless.
Although preexisting standards and solutions are currently impeding that shift to paperless, fortunately, it’s not an insurmountable task. All it takes is a small group of people—within a company or across the industry—to start making changes.
“At the end of the day, the data that’s behind a paper document is not that different. It’s just the application, the means, the processes, the people that all get in the way,” Petrocelli said.
This post was written by Kristin Rawlings. Kristin is a writer, editor, and fierce advocate of the Oxford comma. She has experience working in journalism, academic publishing, and content marketing. Her passion is to read and create well-researched texts, as well as to collaborate with others to share information in a clear, readable way.
Ready to transform your supply chain?
Increase efficiency and productivity. Say goodbye to delays, handwriting errors, and time-intensive manual data entry.