Just in Time (JIT) Logistics, Explained in Detail
In this article, we'll discuss its details, benefits, and drawbacks, and you'll learn how you can prepare so you can implement it successfully.
Ready to transform your supply chain?
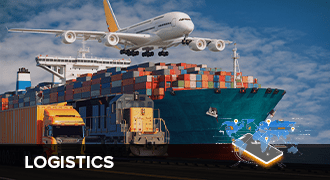
Just in Time (JIT) logistics is an inventory management strategy that aims to deliver goods immediately before they’re needed for the next stage in the logistics process
How JIT Works
Think about how an item usually moves through various steps in the supply chain process. For example, a driver may deliver a finished manufactured item for storage at a warehouse. Then later, the item’s manufacturer may ship it to the customer from the warehouse. The idea behind JIT logistics is to ensure that the item arrives at the warehouse at the moment the manufacturer can ship it to the customer. Thus, Just in Time logistics aims to minimize inventory (which can be expensive to store), reduce delivery time, and eliminate any wastage, such as unneeded items. The firm can potentially manufacture, store, or ship an item when a customer needs one and not before.
Origins of JIT
Like many other management practices, the Just in Time philosophy originated in Japan in the 1970s. Toyota was the first company to apply it and perfect it for manufacturing processes. JIT helped Toyota achieve a high level of efficiency in manufacturing. Over the last few decades, organizations over the world have adopted the technique. Firms have also adapted it for various aspects of the logistics process.
Benefits of Just in Time Logistics
Let’s look at some of the benefits and strategic advantages that Just in Time logistics provide.
Benefit 1: Reduced Inventory
The most obvious benefit of Just in Time logistics is reduced inventory throughout the supply chain. If the item arrives just before the start of the next process, then theoretically there’s no need for any inventory. Of course, in the real world there are always some inventory requirements. But they are dramatically reduced if the firm successfully implements the JIT process.
Benefit 2: Lower Operational Costs
One of the effects of reduced inventory is the corresponding reduced inventory storage costs. Storing and managing inventory is costly. And every extra minute spent in inventory between deliveries means added costs. Thus, reducing the number of goods stuck in inventory helps minimize operational costs and increase profit margins.
Benefit 3: Faster Deliveries
Another consequence of reduced inventory is a shorter waiting time at inventory. If the sub-processes take the same time as before, but the waiting in between each step in the process gets shorter, then the total time to delivery will also get shorter. Moreover, JIT operations focus on constantly minimizing wasted time. That’s literally in the name, in case you forget! Thus, Just in Time logistics helps optimize lead times and enable faster fulfillment.
Benefit 4: Better Responsiveness
Having JIT capabilities enables a firm to be more responsive. Managers can quickly modify the supply chain to suit new demands. Shorter lead times mean it’s possible to fulfill many orders on short notice. Thus, the firm can satisfy different customer requirements. The flow of goods across the supply chain becomes more flexible and adaptable.
Of course, JIT has some drawbacks too.
Challenges of Just in Time
There are undoubtedly many benefits to implementing Just in Time logistics. The inventory requirements are lower, and delivery times are faster. However, just like all things in life, there are challenges as well.
Challenge 1: Difficulty of Accurate Demand Forecasting
Implementing Just in Time logistics is impossible without accurate demand forecasting. Firms need to predict the demand for an item and how it will change over time. This information helps managers to plan the inventory and delivery to ensure on-time fulfillment. If the actual demand is much lower than the forecast, then the inventory will increase. If the actual demand is much higher than the forecast, then the supply chain won’t have enough stock to deliver the items on time. Thus, firms need to rely on data models to accurately forecast demand.
Challenge 2: Possibly Severe Impact of Minor Disruptions
Usually, firms have buffer stock at various points in the supply chain. So if there’s a delay in one part of the process, the buffer helps to offset the inventory shortage for the later steps. However, with Just in Time, the buffer stock is minimized as much as possible. Thus, one small disruption can quickly spread throughout the supply chain. One delay early in the process can disrupt all the corresponding steps. Therefore, businesses need to find the optimum level of safety stock and deal with shipping variance.
Challenge 3: Hidden Costs
Implementing Just in Time logistics comes with various hidden costs. Training the people and building the technology infrastructure to support Just in Time logistics is an expensive investment. In the case of any supply shortages or delays, JIT can lead to unexpected costs. If the supply chain can’t cope with the fluctuations and has regular disruptions, then these unexpected costs can rise steeply.
Now that you’ve had a chance to weigh the pros and cons, are you interested in trying JIT?
Implementing JIT Logistics
Just in Time logistics are a dream when everything works well, but they can turn into a nightmare when things go south. Hence, it’s critical to prepare your organization thoroughly before taking this step. Consider these issues before you dive in:
- Will JIT be a value-added proposition for your firm?
- Will the cost savings be significant?
- Can your employees handle the new work process?
Let’s explore practices you can adopt to prepare your firm for JIT.
Practice 1: Identify Bottlenecks and Inefficiencies
First, thoroughly break down your entire process flow map. Once you map out all the components of your supply chain, you can analyze it in detail. This will help you identify the bottlenecks, holdups, and inefficiencies. The analysis will also help you find the optimum inventory levels in various locations. You can examine your historic data to identify where you can minimize lead times and inventory costs. You can also calculate the delivery times and waiting times throughout your supply chain.
Practice 2: Become Data Savvy
Collecting, storing, and analyzing data is an essential part of the Just in Time logistics strategy. Constant measurement of various key performance indicators helps you make sure you’re meeting your targets and predictions. And when there’s an inevitable issue, you’ll be able to identify it much earlier.
In a constantly changing world, you’ll need to continuously track and improve the process. Thus, making data-driven decisions will help you keep the supply chain optimized for JIT. Moreover, you should strive for seamless communication and data sharing between the different stakeholders. Becoming data savvy is key for Just in Time operations.
Practice 3: Design the Process in Detail
Next, you can design a more streamlined and efficient process. This includes the entire supply chain, from sourcing and production to shipment. You should know the triggers for each task in the process. Ask yourself:
- When does packaging the item start?
- When do you refill the buffer stock in the warehouse?
- How much inventory do you need for each product, and where will you store it?
A detailed process design will help you accurately calculate all these decisions.
Practice 4: Manage the Risk of Disruptions
It’s also important to manage your risk. Even though your forecasts may be accurate, you need to prepare your supply chain to deal with sudden fluctuations. It may seem tempting to reduce inventory even further and achieve almost no waiting time, but in that case, even a tiny issue can wreck your entire supply chain. This is called the bullwhip effect. Even small movements at one end of the bullwhip create vigorous movements at the other end. Similarly, the effects of a small delivery delay can ripple throughout your logistics process. Thus, it’s always advisable to add some safety buffer to your Just in Time calculations.
Is JIT Worth It?
Implementing Just in Time logistics is challenging. However, the efficiency and cost savings can make the investment worthwhile. Thus, spend some time considering if it makes sense for your company. To learn more, check out this logistics guide. [~~~LINK TO COME~~~] It’ll help you plan and implement a Just in Time logistics process for your organization.
This post was written by Aditya Khanduri. Aditya currently handles product and growth at Cryptio.co, and he’s also built a couple of B2B products. He’s proficient in data analysis with Python and has worked with multiple startups in the blockchain and artificial intelligence sector.
Continue reading
Ready to transform your supply chain?
Increase efficiency and productivity. Say goodbye to delays, handwriting errors, and time-intensive manual data entry.