2023 State of Yard Management Report
Bringing the yard up to speed doesn’t just help meet revenue goals; it improves the efficiency of the entire supply chain and lessens the stigma of the yard being the “black hole” of logistics.
Ready to transform your supply chain?
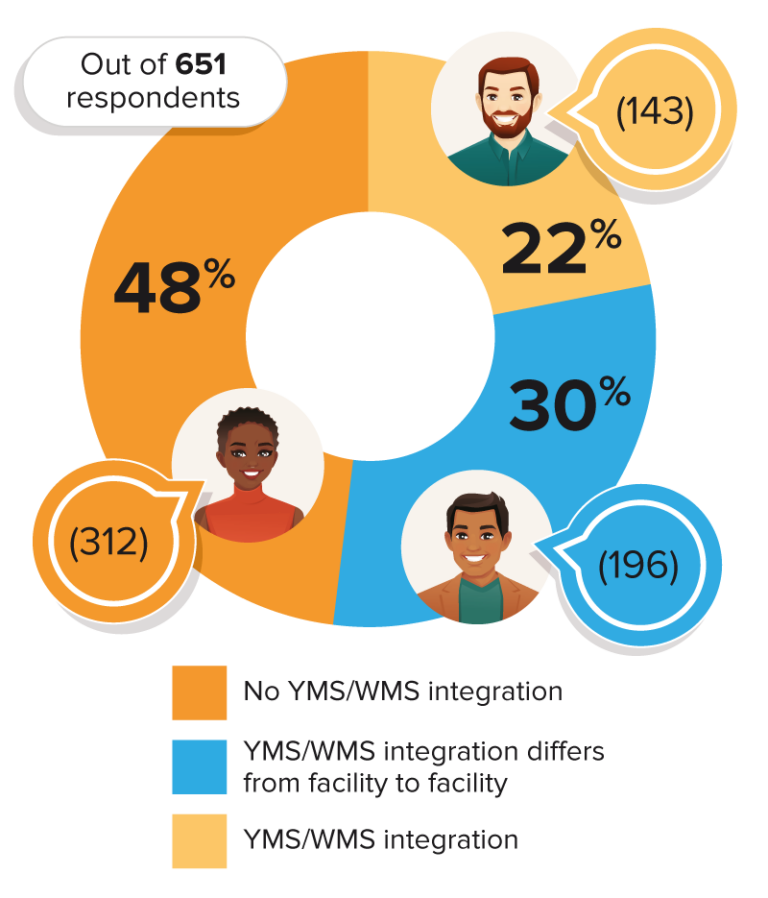
But … we didn’t say it was easy. Heck, we didn’t even say how it can be done. In fact, this isn’t really about any of that anyway!
This is a guide for logistics professionals — like you — to benchmark priorities and yard operations against peers in the industry. AKA, find out how your yard operations and management strategies stack up against the current yard management gurus (and the rest).
CHAPTER 1: State of Yard Management Overview
So, a YMS can help you manage your yard effectively, but what do you need from your YMS partner? To get some answers, ask yourself these questions:
Key Findings Summary
Survey results analysis: Yard management is the thing everyone recognizes is needed, but it’s often overlooked in favor of addressing other mission-critical pain points.
For example, when asked, “What percentage of your facilities use a yard management solution?”
374 (58%) of the 651 respondents said 23% or less of their facilities had a YMS.
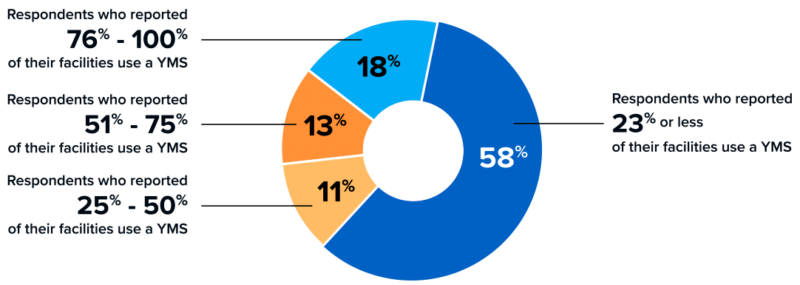
Demographics: Where Did This Data Come From?
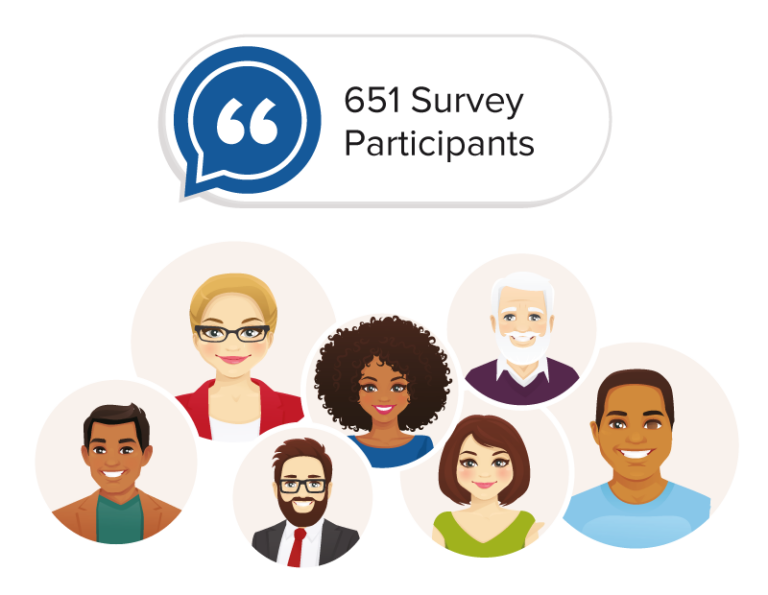
Respondents included medium to enterprise-sized organizations. The 651 survey participants from these companies primarily range from management and logistics.
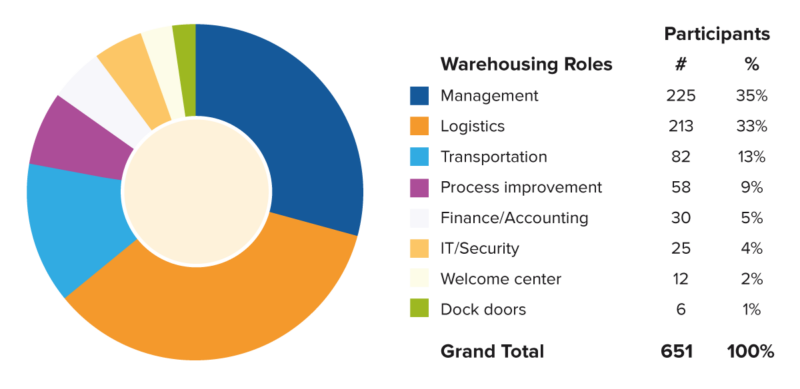
WHEN ASKED
“What are the challenges faced by yard management?”
the top 3 responses were:
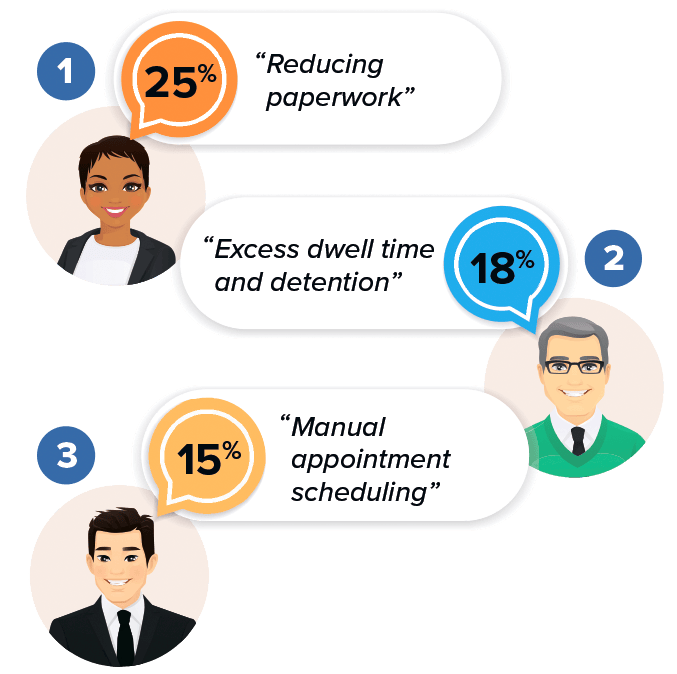
While YMS software can help with all three of these top challenges, 226 survey respondents said that their company not having enough resources could prevent improvements from being made. Another 112 of those surveyed said that there may not be enough in the company budgets to address these challenges.
How many respondents said every aspect of their yard is running smoothly? Less than 10% were in that enviable position!
Supply Chain Management Review reported that there’s “more interest in YMS on the part of shippers that want to get better visibility into their yard and dock activity.” The reasoning behind searching for the right YMS software (and what that software may look like) can be pulled apart and analyzed by looking at more survey results — which is exactly what comes next, and you don’t even have to buy us dinner (but we will buy YOU a cup of Joe if you participate in our next survey, so keep your eyes peeled!)
CHAPTER 2: State of Yard Management Results
The State of the Yard Right Now
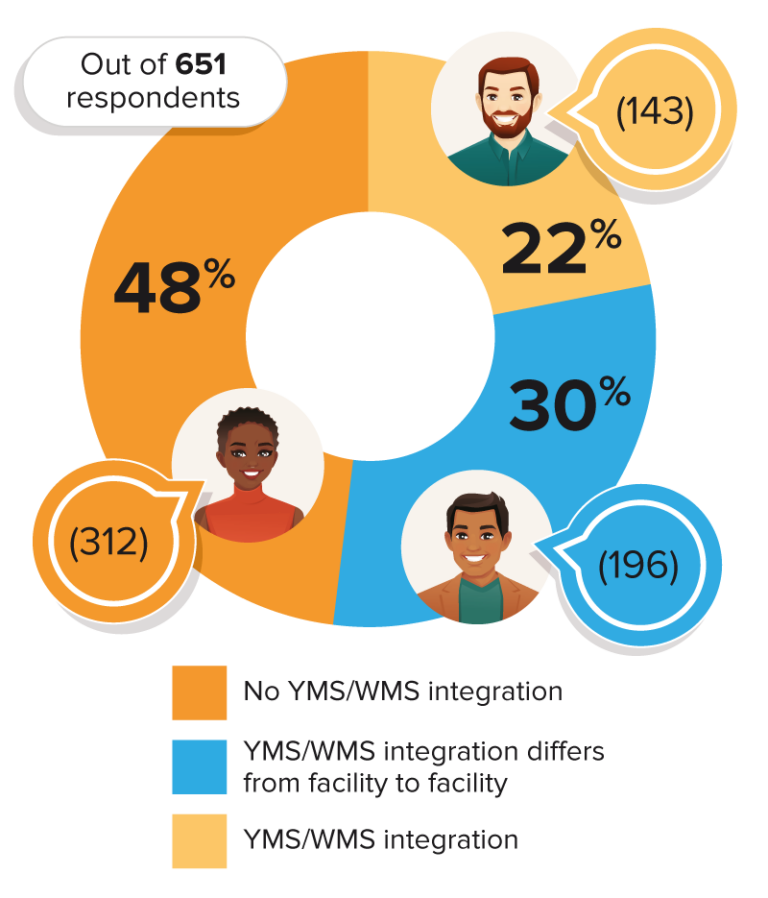
Systems Integration
The Stats: Nearly half of surveyed respondents reported that there is no integration between their YMS and WMS systems, while 30% stated that systems integration differs from facility to facility. With disparate systems posing one of the top challenges to yards today (more on that later), you have to wonder what is stopping companies from bridging that pesky divide for good.
The Take Away: There was a positive correlation between those whose company had 11 or more facilities and the percentage of those facilities that use a YMS. However, the data doesn’t indicate that the YMS is effectively utilized.
For the company facilities that do use a YMS, only 22% of respondents stated that their YMS is integrated with their WMS. Meanwhile, more than twice that number said there was no integration, and the remaining 30% said it differs from facility to facility, creating dreaded data silos.
Facilities That Have a Guard Shack
The Stats: Considering many facilities have not incorporated yard management software, you would think the guard shacks would be everywhere! Interestingly, this is not exactly the case.
For the 77% of respondents who reported they have less than 21 facilities, the percentage of their yards with a guard shack are:
For the 23% of respondents who reported they have more than 21 facilities, the percentage of their yards with a guard shack are:
More than half say guard shacks are at 24% or less of their facilities. Only 11% reported at least 76% of their facilities have them.
The Take Away: Based on the data, there is no evidence that using a YMS can reduce a yard’s dependencies on guard shacks.
While we believe this is a key benefit of a YMS platform, it cannot be substantiated from this survey.
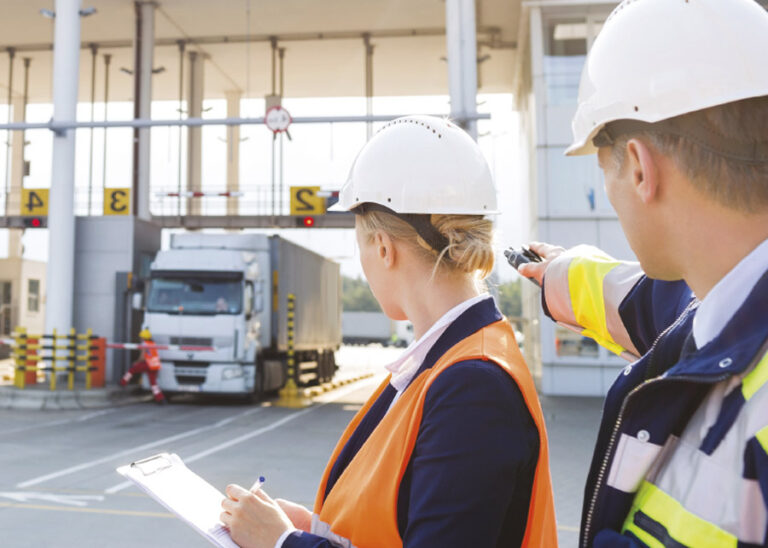
Top Challenges Faced By Yards
Let’s take a closer look at the challenges faced by yards today.
Participants were asked to select the top 3 challenges currently plaguing their yard. The results were as follows:
Reducing Paperwork
Reducing paperwork is the top challenge, with 46% of the survey respondents reporting this as one of their top 3 biggest sticking points.46%
The Take Away: Based on the data, there is no evidence that using a YMS can reduce a yard’s dependencies on guard shacks. While we believe this is a key benefit of a YMS platform, it cannot be substantiated from this survey.
The Dreaded Dwell Times
It makes sense then that 41% of respondents chose excess dwell time and detention as one of their company’s top challenges.41%
Excess dwell times and detention periods hurt your bottom line. They suck the money right out of every logistics partner involved in the supply chain. Having to cough up the fees for delayed delivery times is a huge roadblock for many.
Manual Appointment Setting
Setting appointments by hand makes it feel like you’re still in the 1980s. You can call, you can show up, or you can put it off for another day.
This is no sane way to run a yard, so it makes sense that 39% of respondents consider manual appointments a problem39%
Lack of Integration Between Disparate Systems
Remember the survey stat that for 30% of surveyed companies, some of their facilities had a YMS and their other facilities did not? Hold our beer. Let’s dive in.30%
The pandemic hit many industries like a frying pan to the face. Companies across the globe had to cut costs and find ways to survive. How did the yards handle it? Well, some only bought what they thought they needed — a kiosk here, inventory software there — and didn’t go all-in with a YMS that could be integrated and used for everything in the yard. Now that things are picking up again, companies are starting to see the benefits of switching to YMS for their facilities, but that transition takes time, planning, and resources.
In the meantime, facilities with disparate systems suffer from duplicate data entry, multiple sources of the truth, and having to export data from various systems to generate reports.
Biggest Challenges to Progress in Yard Management
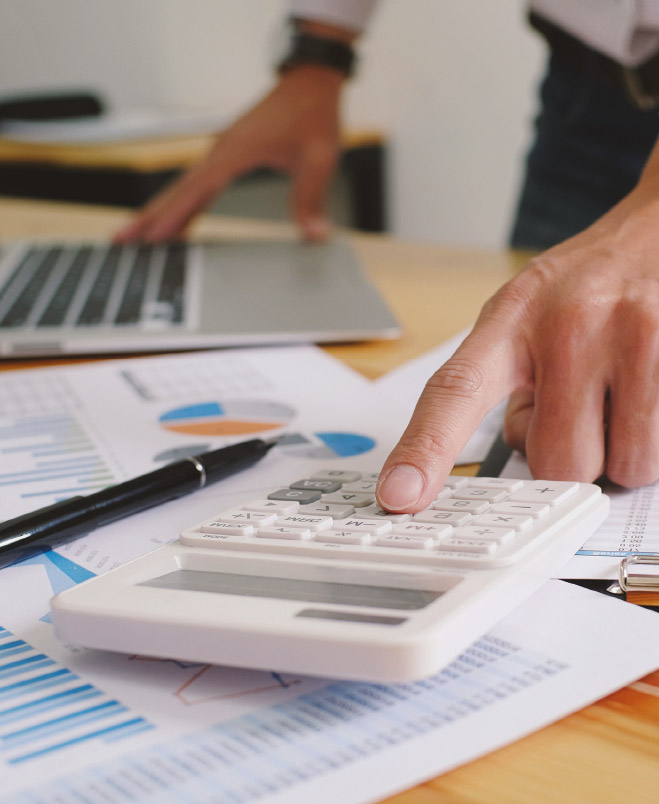
Yards across the world understand the challenges they face and the threats those challenges pose to progress. But how do they solve them? There are several roadblocks:
Not Enough Resources
More than a third of yard managers and company executives can’t justify the upgrade because they don’t have the time or the people needed to develop a plan that key stakeholders would buy into.
Assuming There’s Not Enough in the Budget
Really cool tech is expensive. It’s right to assume that useful software will probably cost a lot, which is why 17% stated that budget is their biggest hurdle. Cost can overwhelm organizations of all sizes, especially if they don’t know how much money they will save by making the switch. And you know what they say about making assumptions.
Management Isn’t On Board
It could be that the research has been done, and the budget is there, but … management isn’t convinced. They may not believe that the juice is worth the squeeze when they weigh the potential benefits of a YMS system vs. the cost and change management involved in making the big switch.
Top Three Logistics Initiatives in 18-36 Months
So what logistics initiatives are (or should be) prioritized? The majority of survey respondents said they are likely to tackle the following challenges faced by their organization within 18 to 36 months:
1 Improve Visibility
The need to improve visibility is apparent, with 74% of respondents stating that this was a top priority in the near future.
TMS and WMS provide the beginning and end of visibility in the supply chain, but something is missing in the middle — YMS. YMS software can act as the watering hole where the supply chain ultimately comes together, closing the gap to get end-to-end traceability
2 Refreshing or Deploying WMS, ERP, TMS, or YMS
A surprising 47% of those surveyed chose management software updates/deployments as one of their company’s top three logistics initiatives.
Improved functionality, streamlined integrations, and strengthened data security are all reasons why teams are opting to upgrade or migrate to efficient cloud systems. However, YMS is often the last in line behind those systems deemed mission-critical, such as WMS, ERP, and TMS.
3 Diversifying or Consolidating Supplier Relationships
44% of respondents stated that diversifying or consolidating supplier relationships was a key initiative going forward.
Yes, you can do both! Which one is worth doing just depends on the current dynamics of the yard. The benefits of prioritizing supplier relationships are practically endless — achieve long-term cost reductions, improve communications for fewer delays, and so on.
CHAPTER 3: What YMS Users Already Know
The 23% that have invested in YMS software seem to know something that other yards do not — an integrated YMS improves multiple aspects of yard management.
Out of 153 companies that are using YMS at more than 50% of their facilities, here are the top 3 benefits they are experiencing at their yard:
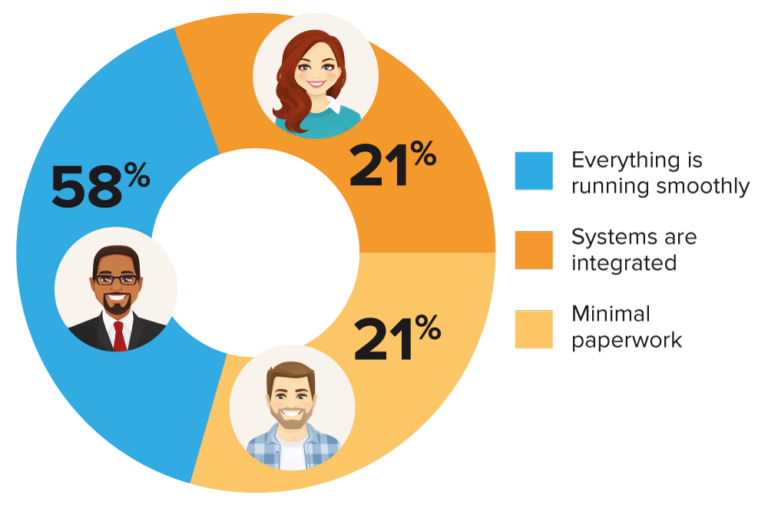
With the middle link of yard management finally integrated with the rest of the supply chain, visibility for drivers, suppliers, shippers, and the yard is a seamless experience that helps to keep everyone on track in real-time. Shippers and suppliers will have access to data they can use to help prevent hiccups and delays. Yards can know when drivers are set to arrive, adjust schedules, maximize yard space, facilitate eBOLs and other documentation for fewer errors, and so much more.
According to Gartner research, over half of the surveyed professionals reported a high level of decision-making automation in the next three years. All things considered, the time to start thinking about smart warehouses, guard-less facilities, and how YMS technology can streamline your facilities is now.
Can YMS Really Do Things?
Here’s the bottom line.
Its time to prioritize yard management as a top supply chain digital transformation initiative.
Why? Because the time to value is quick, the change management is minimal, and requires little to no IT resources to deploy.
Find out how Vector can make yard life easier.
Contact us for more information or a free yard audit.
Continue reading
Ready to transform your supply chain?
Increase efficiency and productivity. Say goodbye to delays, handwriting errors, and time-intensive manual data entry.